Labeling machines are vital to any business as they accurately and efficiently apply information such as product names, ingredients, and warning labels to products. However, the development process of labeling machine on the market have gone through a long time, and selecting these machines can be challenging, and there are many factors to consider.
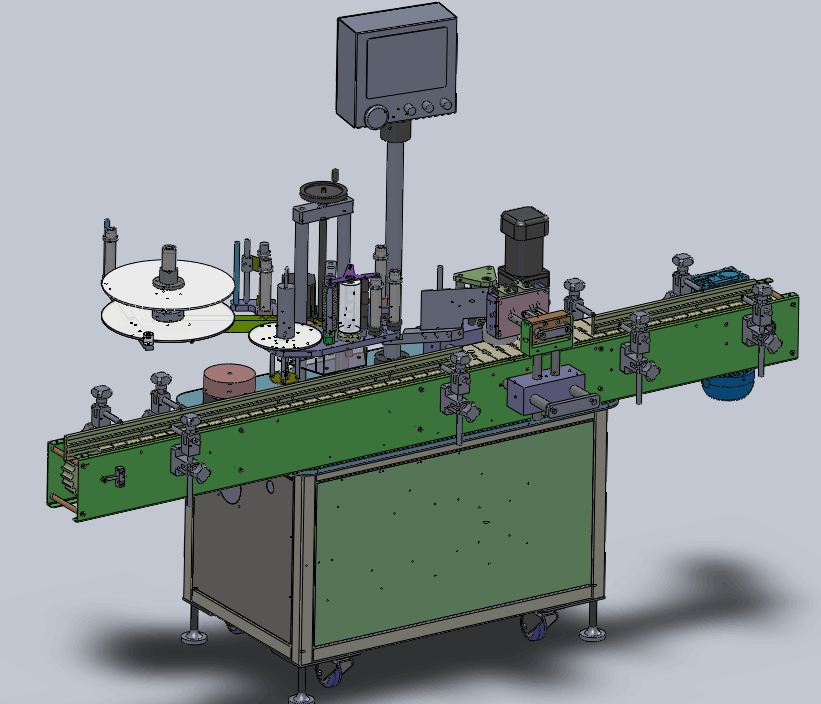
Development Status of Labeling Machine
The development status of labeling machines is affected by many factors. The following are some key considerations that aid in the development of labeling machine:
- Industry Requirements: Different industries have specific labeling requirements based on the products they produce. Labeling machines have been developed to meet the specific needs of these industries, such as food and beverages, pharmaceuticals, cosmetics, and consumer goods. Understanding industry regulations, standards, and labeling guidelines is critical to developing the right machine.
- Bottle or Container Type: Labeling machines must accommodate different bottle or container shapes, sizes, and materials. Development involves considering machine compatibility with various bottle types, including round, flat, square, oval, or custom-shaped bottles.
- Labeling Technology: The labeling machine uses various technologies, such as pressure-sensitive adhesive labeling, glue labeling, or heat shrink labeling. The development process includes selecting the appropriate technology based on label material, bottle material, production speed, and required label placement accuracy.
- Speed and Efficiency: Production efficiency is important for labeling machine development. Labeling machines should be designed to operate at high speeds while maintaining accuracy and consistency in label placement. Developments have focused on optimizing machine performance, minimizing downtime, and incorporating automatic label changing or adjustable speed control features.
- Label Accuracy and Alignment: Labels must be applied accurately and properly aligned on the bottle or container, and the labeling machine should provide adjustment options to accommodate different label sizes and maintain consistent alignment. Development involves incorporating mechanisms to ensure precise label placement, such as sensor-based detection systems, guide rails, or rollers.
- Integration with the Production Line: Labeling machines are usually part of a large automated production line. Development must ensure seamless integration with other machines, such as filling, capping, or packaging systems. Communication protocols, synchronization functions, and control interfaces were developed to facilitate a smooth production flow and coordination with other equipment.
- Compliance and Safety Standards: Labeling machines must comply with safety standards and regulations to ensure operator safety and product integrity. Development involves integrating safety features such as emergency stop buttons, guard mechanisms and adhering to electrical and mechanical safety standards.
- Ease of Operation and Maintenance: User-friendliness is important in developing labeling machines. Machines should be easy to operate, with intuitive controls and user interface. Maintenance requirements should be kept to a minimum, and provisions for easy access to components and regular servicing should be built into the design.
- Cost and Budget Constraints: The development must consider the cost-effectiveness of the machine while meeting the required specifications. Manufacturers strive to balance functionality, quality, and affordability to meet the needs of different market segments.
By considering these factors during the development process of labeling machine, labeling machine manufacturers can create machines that meet the needs of the industry, provide efficient labeling solutions, and ensure customer satisfaction.
Development Process of Labeling Machine
The development process of labeling machine involves several stages, from concept to production.
- Requirements Analysis: The first step is to gather requirements by understanding the specific needs of the target industry and customers, including identification of bottle or container type, label size, production speed, accuracy requirements, integration with existing production lines, and any regulatory or safety considerations.
- Conceptual Design: According to the demand analysis, the design team conducts a conceptual design for the labeling machine, which involves determining the overall structure, components, labeling technology, and control system of the machine.
- Detailed Design: Once the conceptual design is approved, the detailed design phase begins, which includes creating precise technical drawings, specifying components, and selecting motors, sensors, actuators, and other necessary components. The design team ensures the labeling machine meets all required specifications and integrates smoothly with other equipment.
- Prototyping: Build a prototype of the labeling machine from the detailed design, allowing testing and evaluation of the machine’s performance, functionality, and overall feasibility. Gather feedback from stakeholders, including operators and production managers, to make necessary design modifications.
- Software Development: If the labeling machine adopts an automated or electronic control system, software development is performed, including programming the machine interface, control algorithm, sensor integration, and communication protocol. The software is designed to provide user-friendly operation, data logging, and diagnostic functions.
- Manufacturing and Assembly: Once the design and prototyping phases are complete, the manufacturing process begins, including sourcing the required components, manufacturing structural elements, and assembling the machine. Implement quality control measures to ensure each unit meets the required standards and specifications.
- Testing and Validation: Assembled labelers undergo rigorous testing to verify performance and functionality, including testing label placement accuracy, speed capabilities, integration with other equipment, safety features, and reliability under varying operating conditions. Any issues found during testing will be addressed.
- Documentation and Manuals: Prepare comprehensive documentation, including user manuals, maintenance procedures, and technical specifications to guide operators and maintenance personnel. Documentation helps users understand machine operation, troubleshoot problems, and perform routine maintenance tasks.
- Training and Deployment: Once the labeling machine has been thoroughly tested and documented, operator and maintenance personnel are trained to ensure the machine operates correctly and personnel understand safety protocols. After training, the machines are deployed in production facilities with ongoing support as needed.
- Continuous Improvement: Since the labeling machine is used in the production environment, operators, maintainers, and customers receive feedback. Analyze this feedback to identify areas for improvement, whether in terms of performance, efficiency, user experience, or reliability. Implement upgrades and enhancements to continuously improve the labeling machine.
Conclusion
The development process of labeling machine required the collaboration of design engineers, software developers, manufacturing specialists, and quality assurance personnel to create a reliable, efficient, and user-friendly machine that met industry requirements and customer expectations.