The automatic capping machine is divided into two main types according to its working principle and movement mode: rotary and linear. The rotary automatic capping machine fastens the cap on the container by rotating the cap. It is generally suitable for small and medium-scale production, especially for production lines that handle multiple varieties. The linear automatic capping machine precisely fastens the cap on the container through linear motion. It usually has a higher degree of automation and can be more easily integrated with other equipment to achieve a fully automated production line.
Rotary Automatic Capping Machine
A rotary capping machine is a key piece of equipment to close containers on an automated production line. It is favored for its unique working principle and function. It secures the lid to the container using a rotary motion, allowing the capping process to be completed relatively quickly. This makes it ideal for high-production lines, helping to increase productivity and throughput.
The rotary capping machine is suitable for various types of caps, whether plastic bottle caps, metal caps, or caps of other materials. All can complete the capping operation on the same equipment with proper adjustments. Machines typically feature a simple operator interface and logic, allowing operators to get up and running quickly.
The rotary capping machine is designed to accommodate containers of different sizes and shapes, and it can simultaneously process products of various specifications on the production line. It is extremely flexible.
The rotary capping machine is not only suitable for large-scale production lines, but also suitable for small and medium-scale production, providing a practical capping solution for small and medium-sized enterprises. Rotary capping machines generally have lower purchase and maintenance costs than some more complex automated equipment. This makes it the choice of many companies to control costs while increasing production efficiency.
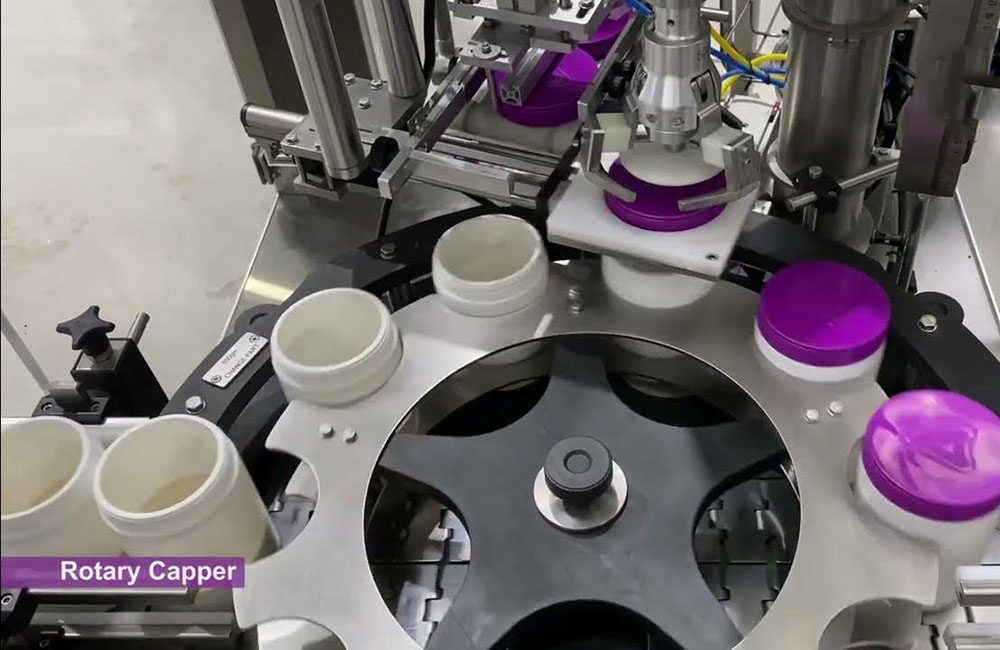
Linear Automatic Capping Machine
Linear capping machines are used for efficient and precise closure of all types of containers. It uses a linear motion for closure, which tightens the closure in very precise positions, ensuring consistent closure quality from container to container.
The design of the linear capping machine makes it suitable for high-speed production lines. The linear motion can quickly complete capping and sealing in a short time, effectively improving production efficiency and output.
Linear capping machines are usually integrated with other automated equipment (such as conveyor belts, filling machines, etc.) to form a highly automated packaging production line. This integration can improve the overall efficiency and consistency of the production line.
For some high-viscosity products, the capping process is more challenging. Linear capping machines can efficiently handle these high-viscosity products through precise motion and control.
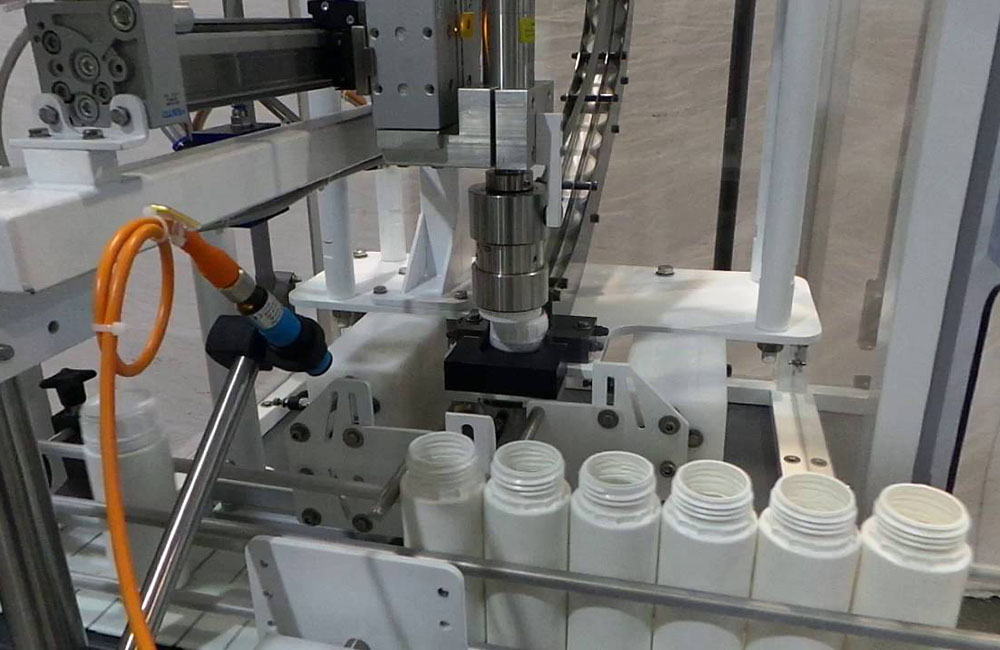
Rotary VS Linear Automatic Capping Machine
In the automated production line, rotary and linear capping machines are two common types of capping equipment. They each have some features and advantages. Here is a comparison between them:
- Exercise Method:
- Rotary capper machine uses a rotary motion to secure the cap to the container, usually by rotating the capping head or cap. This type of movement is suitable for various cover types and is characterized by high efficiency.
- Linear capping machine uses linear motion to precisely fasten caps on containers. The linear motion makes the capping process more precise and suits products requiring high consistency.
- Scope of Application:
- Rotary capping machine is suitable for different cap types and container sizes, with high versatility, suitable for multi-variety production.
- Linear capping machine is suitable for high-speed production lines and precise capping requirements, especially for high-viscosity products and products requiring high-quality closures.
- Production Efficiency:
- Due to the high efficiency of the rotary motion, the rotary capping machine is suitable for high-efficiency small and medium-sized production lines.
- The linear capping machine is suitable for high-speed production lines, can complete more capping operations quickly, and is suitable for mass production.
- Degree of Automation:
- Rotary capping machines can be integrated into automated lines easily, but it requires additional ancillary equipment for full automation.
- Linear capping machines can integrate with other equipment easily and achieve a higher degree of automated production.
- Precision and Consistency:
- Rotary capping machines, while efficient, maybe slightly less accurate and consistent than linear capping machines.
- Due to the linear motion, the linear capping machine can achieve higher precision and consistency, especially suitable for products requiring high quality closure.
- Equipment Cost and Maintenance:
- Rotary capping machines usually have a low purchase cost and are suitable for small and medium enterprises.
- Linear capping machines may have a higher purchase cost due to the advantages of precision and consistency. It can improve product quality, thereby reducing the occurrence of follow-up problems and reducing maintenance costs.
- Applicable Industries:
- Rotary capping machine suits many industries, such as food and beverage, cosmetics, and daily necessities, especially for small and medium-scale production.
- Linear capping machine suits pharmaceutical, chemical, high-speed production lines, and other industries requiring precise and efficient capping.
Conclusion
When choosing a rotary or linear automatic capping machine, manufacturers must consider factors such as production needs, product characteristics, production line layout, and budget. Each type has applicable scenarios and advantages, and choosing a suitable type will help improve production efficiency and product quality.